Labor Shortage in Industry: How Businesses Are Tackling the Lack of Skilled Workers
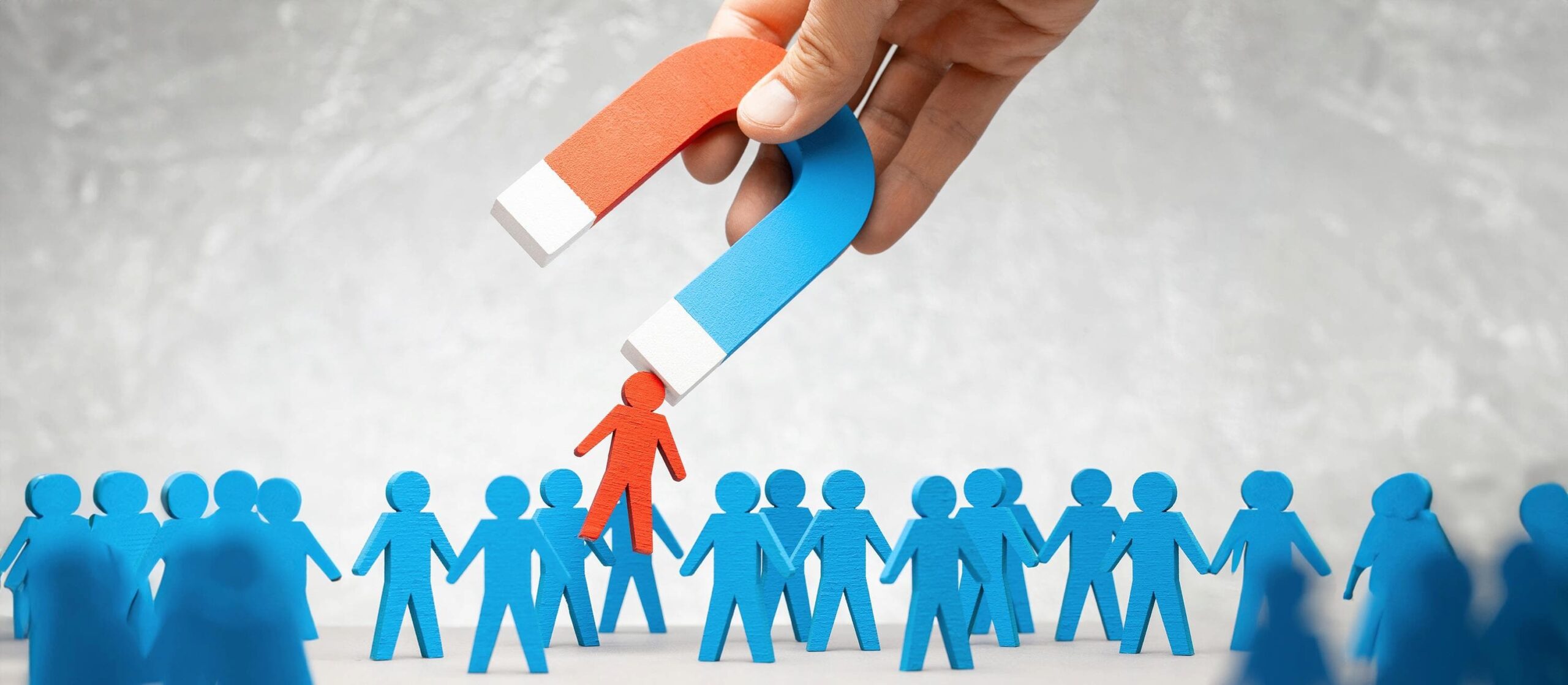
Industry remains a key driver of the economy, but today it faces a serious challenge — a sharp shortage of qualified personnel. Hungary, like many other EU countries, is experiencing a deficit of engineers, technologists, skilled workers, and IT specialists, which hampers the development of enterprises. This situation is unfolding amid rapid technological transformation, where traditional industries increasingly demand complex skills from employees. Why is this happening, and what strategies help businesses attract and retain staff in a highly competitive environment?
Causes of the Labor Shortage in Industry
One of the main causes of the shortage of specialists is the demographic decline, which is particularly noticeable in Central European countries. The population of Hungary, like many European nations, is aging, and young people are increasingly reluctant to choose technical professions. Sociological studies show that many high school graduates view industrial professions as physically demanding and low-paying, preferring service sectors, IT, or public administration.
Another significant factor is the technological gap between education and the actual needs of businesses. Modern enterprises require specialists who understand automated production lines, the industrial Internet of Things (IIoT), and predictive analytics systems. However, technical universities and colleges often lag behind these requirements by 5–7 years. As a result, companies are forced to train employees after hiring them, which increases costs.
Competition for qualified personnel among companies also exacerbates the problem. Large international corporations operating in Hungary offer not only high salaries but also additional benefits such as corporate housing, health insurance, and relocation programs. Local manufacturers often cannot compete with these conditions, losing valuable specialists.
How Businesses Are Addressing the Labor Shortage
Industrial enterprises in Hungary are applying a comprehensive approach to solving the labor shortage. One of the most effective tools has been deep cooperation with educational institutions. Leading Hungarian companies, such as Audi Hungaria and the petrochemical holding MOL Group, actively invest in modernizing the laboratories of technical universities. They not only provide modern equipment but also participate in curriculum development to ensure that graduates come to production with up-to-date knowledge.
Special attention is given to dual education, where students combine theoretical learning with on-the-job training. This approach has already proven effective in Germany and Austria and is now actively being implemented in Hungary. Companies gain motivated employees familiar with the specifics of production, while students receive a guaranteed job after graduation.
To retrain existing staff, enterprises are creating corporate training centers. For example, the Dunaújvárosi Acélművek steel plant has organized its own academy, where experienced workers take courses in automated systems management and the basics of cybersecurity. These programs help retain valuable personnel by adapting their skills to new technological realities.
Attracting Foreign Specialists and Automation
Given the limited local labor force, industrial companies are increasingly turning to the international labor market. Hungary, as an EU member, has access to the pan-European employment system, which simplifies the hiring of specialists from other Union countries. Mechanical engineers, chemical production technologists, and automation specialists from Poland, the Czech Republic, and Slovakia are especially in demand.
For workers from third countries, including Serbia, Ukraine, and the Balkan region, simplified labor migration programs are in place. Many companies offer relocation packages that include housing assistance, language courses, and family adaptation support.
At the same time, active industrial automation is underway. The introduction of industrial robots and artificial intelligence systems helps offset the lack of manual labor in repetitive operations. However, this process requires significant investment and creates demand for new specialists — operators of robotic systems, maintenance engineers, and programmers.
Prospects and Challenges for Hungarian Industry
The labor crisis in industry is a systemic issue that requires coordinated action from businesses, the government, and educational institutions. In the medium term, the key direction will be further development of dual education and corporate training programs. Positive changes are already evident — more young people are considering technical specialties as promising career paths.
Government support also plays an important role. The Hungarian government implements retraining subsidy programs and tax incentives for companies investing in automation. Special attention is given to regions with traditionally high unemployment, where training centers are being established to prepare specialists for the needs of local enterprises.
In the long term, success will depend on the industry’s ability to offer attractive working conditions and career growth opportunities. Companies that can combine modern technologies with effective HR policies will gain a significant competitive edge. For Hungary, this is an opportunity not only to overcome current challenges but also to strengthen its position as one of Central Europe’s industrial hubs.
Modern industry is undergoing a period of transformation, and the labor issue remains one of the most pressing. However, the experience of leading Hungarian companies shows that a systematic approach to training and retaining specialists can yield positive results in the coming years.